Boost Impact Wrench Performance with Torque Testers
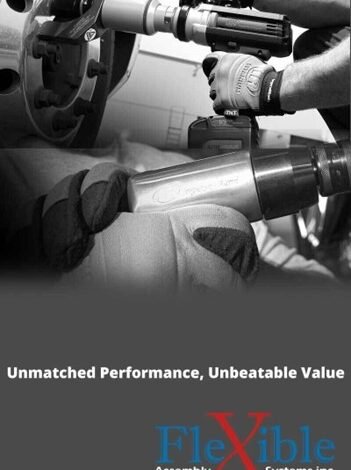
Impact wrenches crank out high torque for blazing fast fastening times. However, speed comes at a tradeoff of accuracy. This matters when torque tolerances reach down to just a few percent. Sure, pneumatic impacts estimate their output – but variation is inevitable.
This is exactly why pairing impact tools with proper torque testers improves assembly quality control. The combo multiplies productivity yet still verifies specifications are met. Read on to learn why this tag team approach works, how to use them together, and the expertise Flexible Assembly offers.
The Need for Torque Precision
First, why is hitting the right torque spec important? For one, safety depends on it. From lug nuts to cylinder heads to airframe bolts, improper torque jeopardizes structural integrity under load. And creators certainly don’t pick torque values randomly. Engineers design assemblies factoring precise clamp loads, material strengths, vibrations and more to derive target figures.
Thus, deviations above or below spec cause real reliability risks. On critical fasteners, just a few pound-feet makes a measurable difference. And unfortunately, pneumatic impact tools inherently lack repeatable accuracy. Their variability requires secondary validation – enter the venerable torque tester.
The Impact Wrench Quandary
Impact wrenches dominate pro assembly shops for good reason. Compared to hand tools, they gulp down major time savings when driving multiple fasteners. Say you need to bolt together heavy equipment or an automotive powertrain. Pulling the impact trigger zips each bolt down far quicker than muscle-powered alternatives.
Mechanics love how air impacts make quick work of stubborn bolts too. Inside lives a hammer connected to the output shaft. As air flows through, this hammer rapidly builds speed then wallops the anvil upon trigger pull. These torque spikes break loose even rusted on hardware with ease.
However, there lies an accuracy issue with impacts. All those internal blows lead to statistical variation in each delivered torque spike. And when tools claim a working torque range – say 100 to 150 ft-lbs – you’ll see random output scattered across that band with each trigger pull.
Sometimes you’ll luck out and randomly hit the needed torque. But testing shows it’s just as likely to come in quite low or high instead. Relying solely on impact tools puts any precision assembly at risk when stuff must be torqued down to a spec.
Bridging the Gap with Torque Testers
Since pneumatic impact drivers inherently lack repeatability, using a separate torque checking device becomes mandatory. These purpose-built tools quantify actual torque applied during final tightening. Many options exist like beam, dial, digital click-type torque wrenches.
But for true quality assurance, nothing beats a torque analyzer that captures reams of data. The latest Bluetooth-equipped varieties record torque, angle, pulse charts and other variables during the life of every fastener. Cloud apps let managers pinpoint any hiccups like botched assembly or faulty components.
A prime example lies with our Torque Testers like the Flex-GT digital torque tester which provides +/-3% full scale accuracy and test modes per J1939. Instead of guessing, now workers KNOW each fastener reached its target torque and angle down to finite detail. Manual torque testing simply cannot deliver this level of precision assurance.
Getting the Most from Impacts
Impact tools deserve ongoing respect in assembly, just need proper management. Here are tips so your shop gains productivity from them while still upholding precision:
- Train workers on proper impact operation – incorrect use hampers performance and life
- Check air hoses and fittings for leaks which reduces power
- Lubricate impact mechanism periodically
- Confirm tools include reaction bars to resist counter-rotation
- Verify torque range still meets stated specs through annual calibration
- Always finish tightening sequence by checking torque with a tester
- Log the torque, angle and pulse data for each fastener tested
In essence, let the impacts blast through the initial tightening stage quickly. But dial things in with a final torque pass using an instrumented tester for confirmation. This failsafe approach brings quality and speed.
Read more: How Do Tech Companies Source Critical CPU Components?
Partner with the Experts
This article explains why assembly shops should upgrade from uncertain impact-only tightening to verified precision. Adopting torque testers like our Flex-GT improves quality while still leveraging the productivity of air tools. For over 18 years, Flexible Assembly Systems has provided advanced fastening and ergonomic solutions to leading manufacturers worldwide.
Beyond cutting edge torque instruments, we also offer:
- Programmable electric screwdrivers
- DC electric and AC servo nutrunners
- Custom fixturing and workstations
- Balancers, manipulators, and lift assists
Fact is, tightening hardware to exact specs has never been more crucial for quality and safety. Contact our engineering team today to discuss how Flexible Assembly can bring you a turnkey precision torque assurance program. Trained application specialists will spec out solutions maximizing operator ergonomics, efficiency and productivity at the highest standards.